Maintenance scheduling
This section of the application is dedicated to managing maintenance notifications, assigning maintenance orders to maintenance technicians or teams, tracking progress and status of maintenance orders, providing overviews of equipment and spare parts, and monitoring the workload of individual technicians.
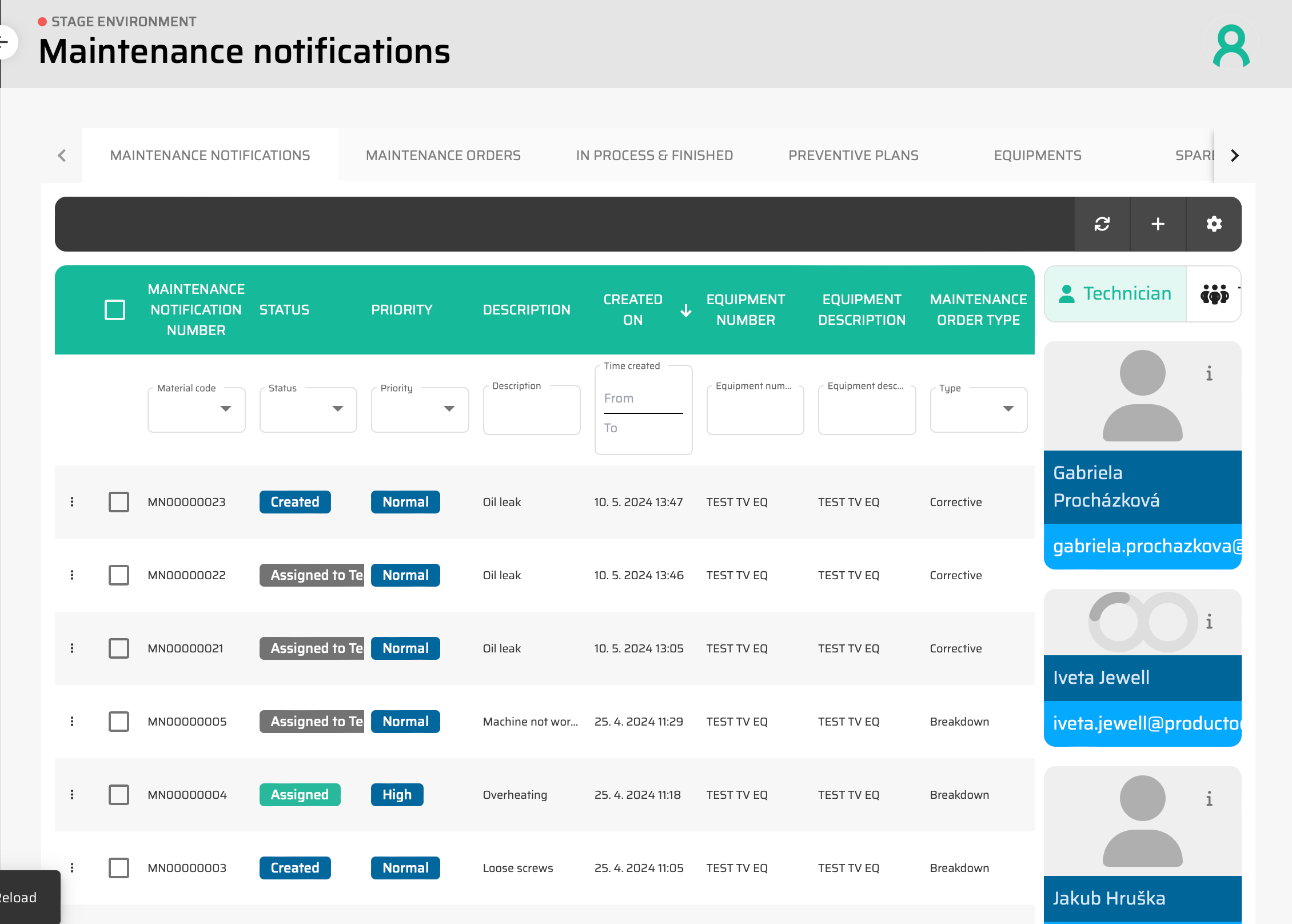
Key Features:
Maintenance Notification Management: Users can create maintenance notifications within the CMMS module. These notifications may include details such as the nature of the maintenance required, priority level, and any associated documentation or notes.
Assignment of Maintenance Orders: Once a maintenance notification is submitted, administrators or designated users can assign tasks to individual maintenance technicians or entire maintenance teams. This ensures efficient allocation of resources based on workload and expertise.
Progress and Status Tracking: The CMMS module allows users to monitor the progress and status of maintenance orders in real-time. From submission to completion, users can track each stage of the maintenance process, enabling timely intervention if necessary.
Equipment and Spare Parts Overview: Users can access comprehensive overviews of equipment stored within the system, including details such as maintenance history, current status, and upcoming maintenance schedules. Additionally, the module provides visibility into available spare parts inventory, facilitating proactive maintenance planning.
Technician Workload Management: Administrators have access to tools for monitoring the workload of individual maintenance technicians. This includes tracking assigned tasks, upcoming schedules, and overall productivity, allowing for optimized resource allocation and scheduling.
Maintenance scheduling is divided into following tabs: