Production line planning
Production line planning involves creating a detailed strategy for the manufacturing process, including determining resources, scheduling tasks, and establishing quality control measures. The goal is to ensure efficient, cost-effective, and high-quality production.
Production queue filters:
a. IDb. Material
c. Production version
d. Quantity
e. Outbound delivery number
f. Goods issue time
g. Required start time
h. Required finish time
i. Created
j. Handling unit template
k. Scheduled finish time
l. Estimated times
The dot shows the items from the bill of materials that make up the product, how many pieces do I need for production? The color indicates the current status of the pieces I have in stock:
Red = there are not enough pieces in stock and neither in planning
Blue = zaplánovaná výroba ale není na skladě - stihne se (materiál BOMu u kterého se to ukazuje)
Green = there are enough pieces in stock immediately
Material change → line reconfiguration (set in the parameterization)
Breaks
Red Scheduled finish time → Line delays
List of individual times used in line planning and where this data is taken from:

Action buttons affecting times in the production plan:
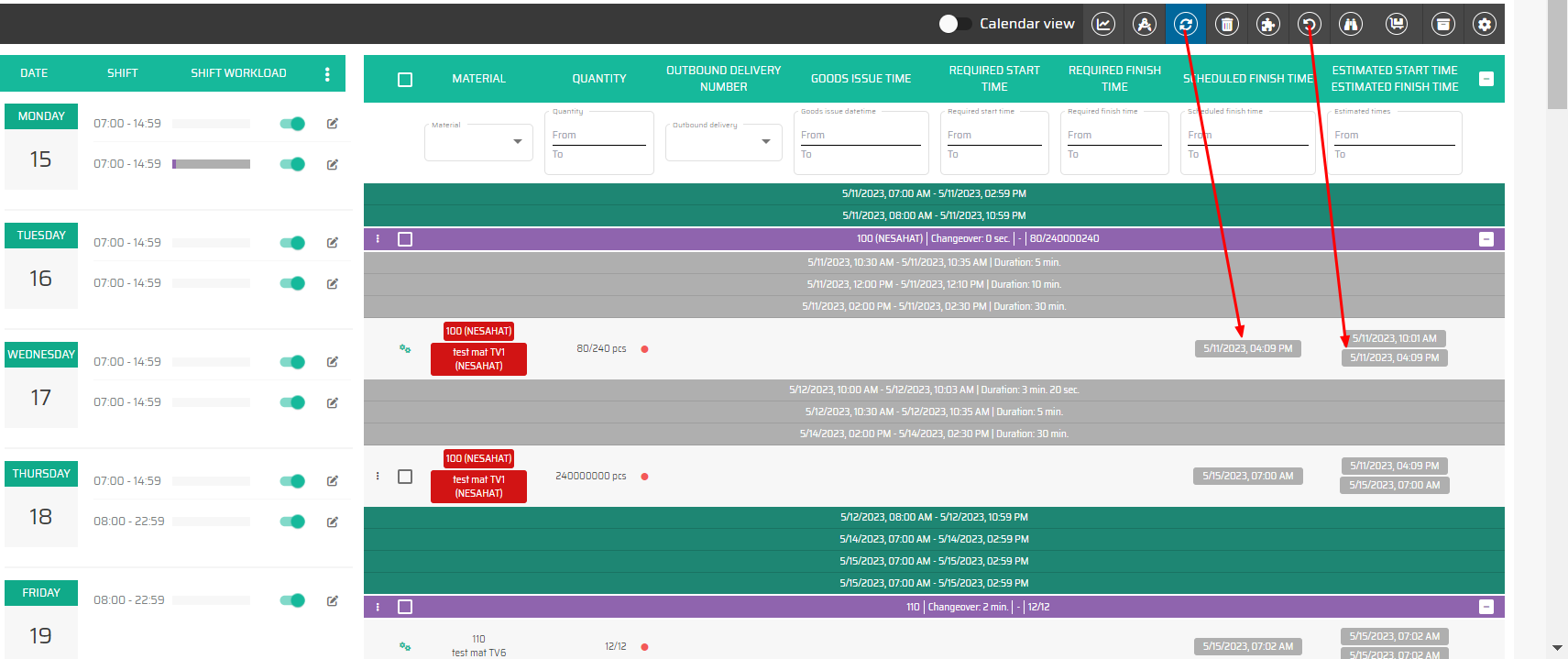
The gray button "Reset estimated times" sets the Estimated Start Time of the first item in the plan to the current time.
Calculated based on the Estimated Start Time according to the production times of the material and the quantity produced for the Work Order (and in the future, based on operator skill level).
Scenarios
We have the ability to generate different options or possibilities and present an overview of each. Based on this, you can evaluate and determine which scenario is the most beneficial for you.
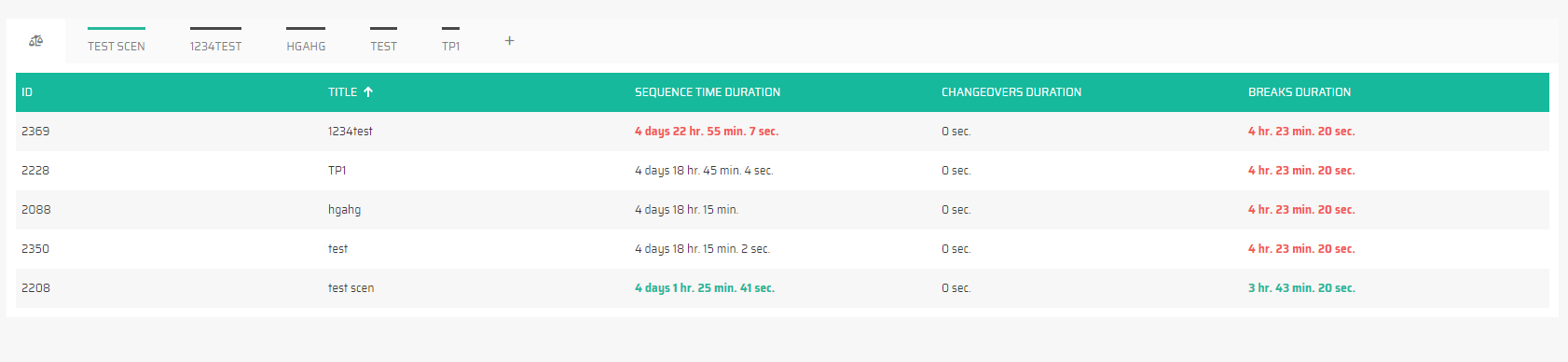
The green scenario is active.
List of currently generated shifts
Here you can see the scheduled shifts for the following days:
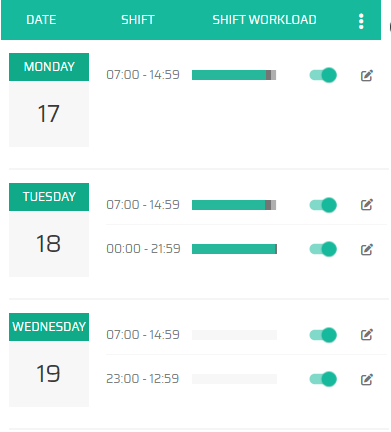
You can simply turn the shift off with :Shutdown:
You can hide the shifts tab with :SHIFT:
Or you can change the following information by clicking on :Change:
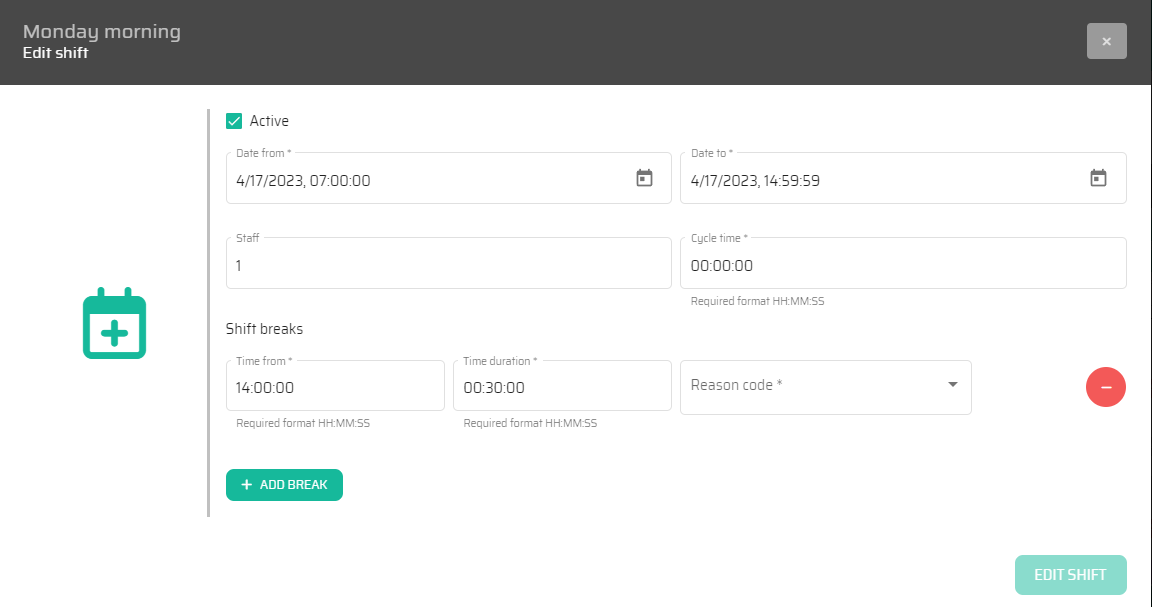
In the main bar, we have the following options:

Action | Description |
---|---|
Create Shift | Manually create production Shift |
Delete Shift | Delete production shifts from selected date |
Calendar / Sequence view toggle | Switch view between sequence liset and calendar |
Update data | Refresh data in planning |
Show Queue Statistics | Display queue KPIs |
Set Planner | Open Artificial Planner options |
Reset Time Difference | Set for all items in queue their Scheduled start and finish times to the same values as their Estimated start and finish times - resets the Delay/Advance of the line. Also regenerate production shifts based on line settings. |
Delete Scenario | Delete this queue scenario (only non-active) |
Batch Building | Open dialog with batch building of this line |
Recalculate Estimated Times | Recalculate Estimated star and finish times |
Show Production Line log | Dialog with detailed log of changes in queue |
View Line Redbox | Redirects to Redbox list pre-filtered by this production line. |
Show hint | Shows color legend for calendar planning |
Customize Table | Open layout settings |