Parametrization navigation
The Parametrization menu is accessible via the Parametrization page on the left side. All the navigation can be hidden and shown again via clicking the arrow in the top right corner of the navigation.
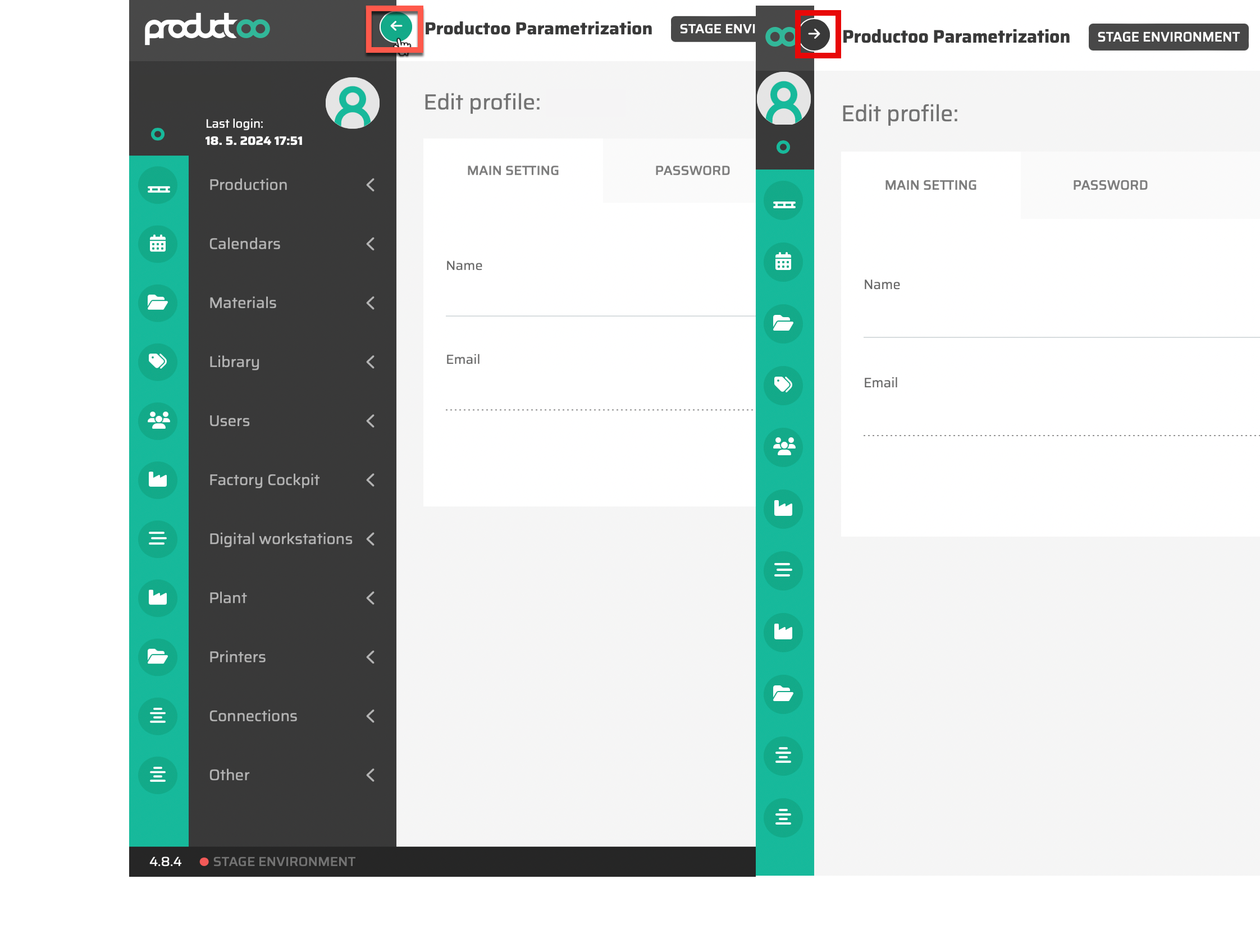
Parametrization navigation is divided into section based on logical grouping of connected objects. Complete structure of the menu can be different for each installation based on the user rights and application available module settings.
All available sections and items are mentioned in the list below:
Production
In this section of the parametrization, we're accessing the possibility to influence the production of the plant. We can create new, edit or delete data for production. These operations can be done in the following tabs:
Calendars
This parameterization section is responsible for defining time schedules such as production shift templates, maintenance preventive plans, and the definition of entire calendars that govern production throughout the year. In this section, you can configure and customize various temporal aspects of the system to align with your specific operational requirements.
Materials
This parameterization section also includes the definition of material master data, spare parts, and handling units. In this section, you can set up and manage the essential information related to materials used in your production processes. The material master data allows you to define attributes such as material type, description, unit of measure, and other relevant specifications. This data serves as a foundation for inventory management, production planning, and procurement activities.
Library
This Library parameterization section is dedicated to defining various supporting entities that enable the full functionality of the application. In this section, you can configure entities such as vendors and customers, units of measurement, equipment, media files, and more.
Users
This application's parameterization section also includes the definition of users, user roles, and user team. This section allows you to configure and manage the user-related aspects of the application, ensuring proper access control.
Factory Cockpit
Factory cockpit is a term used in industrial automation to refer to software or a system that is used to manage and monitor operations in a factory or other industrial facility. The factory cockpit allows operators to view and track real-time data on production and processes, enabling them to quickly respond to any issues and optimize the performance of machines and equipment.
Digital Workstation
Digital Workstations are screens intended for the execution of actions and the monitoring of key information in the company's production and logistics space. The following screens can be defined:
Plant
This application's parameterization section also encompasses the definition of warehouses, internal logistics rules, and the Truck Images feature. This section allows you to configure and manage various aspects related to inventory management and logistics operations.
Printer
This parameterization section of the application also includes the definition of rules for printing production labels and printer settings. This section allows you to configure and customize the printing process to meet your specific requirements.
Connections
This parameterization section also includes a dedicated component for managing imports and exports with external systems. This section allows you to define and configure the available import and export functionalities that facilitate data exchange between the application and external systems.
Others
This parameterization section of the application encompasses a range of global settings that have application-wide implications. This includes the configuration of connections to external systems, password policies, process settings, and the screen splitter feature.