Outbound Delivery return
In the P4 system, there may be instances where a customer returns a previously shipped item. To manage this process, the system allows you to efficiently reintegrate the returned material back into inventory. This ensures accurate stock levels and maintains the integrity of your inventory records.
Step-by-Step Guide to Processing a Material Return
1. Navigate to Production Control
To start the return process, access the Production Control module within the P4 system. This module is central to managing various production and inventory tasks, including handling returns of shipped items.
Location: Production Control Module > Deliveries Section > Outbound Deliveries
2. Select the Relevant Delivery
In the Outbound Deliveries section, identify and select the delivery corresponding to the item that has been returned by the customer. This ensures that the correct shipment is updated in the system.
Action: Click on the specific delivery entry related to the returned item.
Outcome: A dialog box will open, allowing you to manage the delivery details.
3. Access the Material Tab
Once the dialog box is open, navigate to the Material tab. This tab provides a detailed list of all materials included in the selected delivery, enabling you to process returns efficiently.
Action: Click on the Material tab.
Purpose: To manage the materials associated with the delivery, including the processing of returned items.
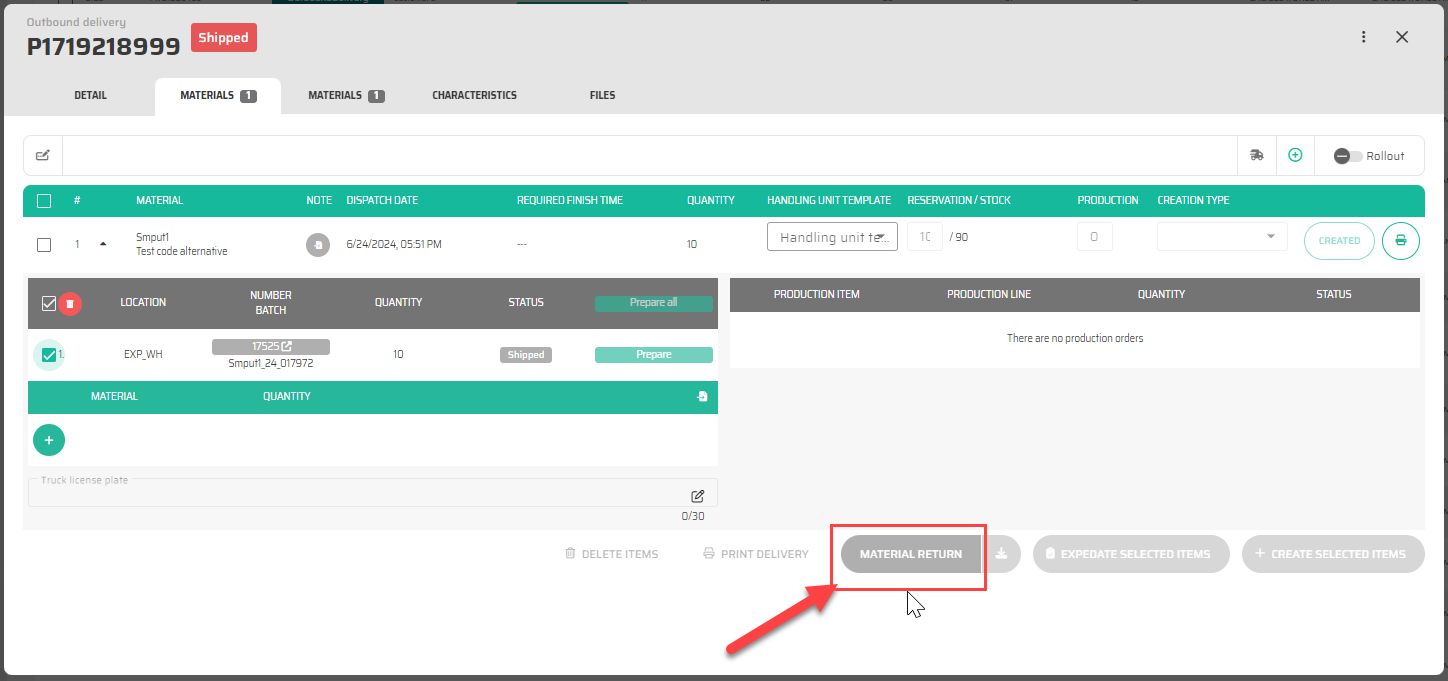
4. Process the Material Return
In the Material tab, you will see a table listing all materials that were included in the delivery. To process the return of a specific item:
Step 1: Identify the material that has been returned by the customer.
Step 2: Select the material by marking the checkbox next to it.
Step 3: Click the Material Return button to initiate the return process.
Outcome: A dialog box will appear, prompting you to enter details related to the return.
5. Complete the Return Details
In the Material Return dialog box, you will be required to provide specific information to correctly reintegrate the returned item into inventory:
Returned Quantity: Enter the quantity of the material that has been returned.
Warehouse: Select the warehouse or storage location where the returned material should be restocked.
Comment (Optional): Optionally, add any relevant comments or notes about the return. This can include reasons for the return, condition of the material, or any other pertinent information.
Action: Once all details are filled in, confirm the return to complete the process.
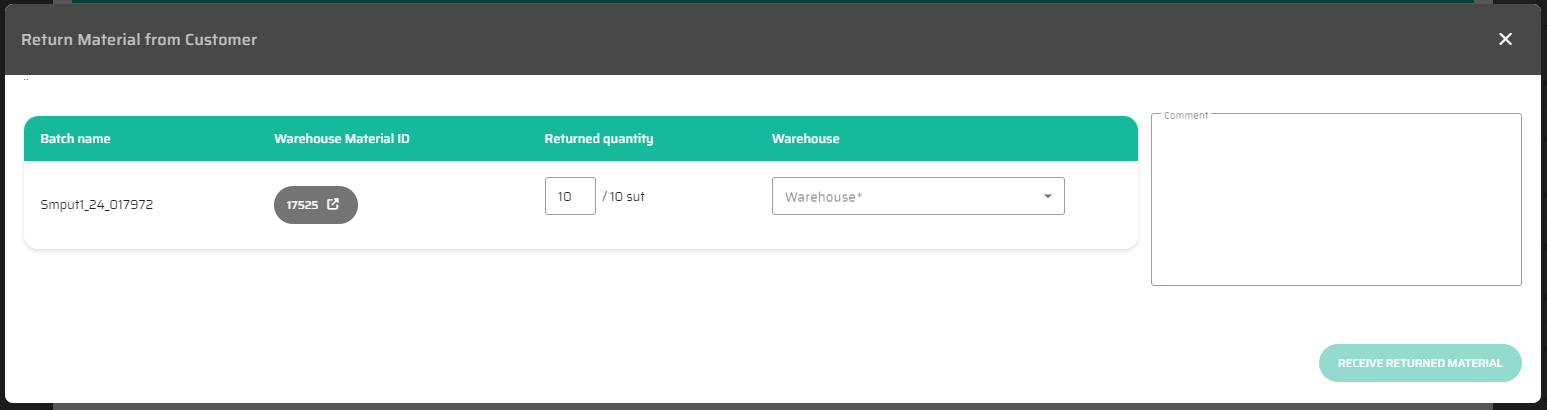
6. Update Inventory
After confirming the return, the P4 system will automatically update the inventory:
Stock Adjustment: The system will add the returned quantity back into the specified warehouse's stock.
Record Keeping: The return will be logged in the system, ensuring that inventory records are accurate and up to date.
7. Verify the Return
To ensure that the return has been processed correctly, it’s advisable to verify the updated inventory levels:
Action: Check the inventory records for the specified warehouse to confirm that the returned material has been added.
Best Practices for Handling Returns
Properly managing returns is critical for maintaining accurate inventory records and ensuring customer satisfaction. Consider the following best practices:
Inspect Returned Items: Before processing the return, verify that the returned material is in acceptable condition for restocking.
Document Returns Thoroughly: Utilize the comment section to document any important details about the return, which can be valuable for future reference.
Coordinate with Inventory Teams: Ensure that the inventory team is aware of the return and any special instructions regarding the restocking of the material.
Troubleshooting Common Issues
If you encounter challenges during the return process, here are some common solutions:
Unable to Select Delivery: Ensure the correct delivery has been selected and that the material is not part of a locked or finalized order.
System Errors During Return: If the system encounters an error when processing the return, check for system updates or maintenance activities and try again later.
Incorrect Inventory Adjustment: If the returned quantity does not reflect correctly in the inventory, review the return process and ensure all steps were followed properly.